Finishing a surface adds value to products, enhancing both aesthetic appearance and component performance. But perhaps the most vital role of a finish is protection. The IEEE estimates that corrosion or structural breakage costs over $100 billion annually in product loss. A great finish provides an effective shield that combats the effects of deterioration-causing elements and damage. Read more
FABTECH 2018 is right around the corner, and here at IntelliFinishing, we’re rehearsing a fantastic educational presentation! This year’s annual event celebrating the best in metal manufacturing is being hosted in Atlanta at the Georgia World Congress Center from November 6-8. Come and join more than 35,000 attendees for demonstrations by over 1,500 exhibiting companies, as well as informative workshops and presentations by thought-leaders on the latest trends and technology in the metal forming, fabricating, welding and finishing industries. You’ll definitely want to mark your calendar for a certain can’t miss discussion – C60 Automation – Is It for Everyone? on Wednesday, November 07, 1:30 PM – 3:30 PM, Room: B301. IntelliFinishing’s John Claman will lead off that session with his presentation on the Levels of Automation for Finishing Systems. Read more
For Caterpillar, the painting process traditionally created a bottleneck in their manufacturing process. The variety and complexity of parts resulted in a wide range of finishing times that often slowed the entire production operation.
About a decade ago, Caterpillar, looking to streamline this process, partnered with IntelliFinishing to develop and install lean finishing systems at seven manufacturing locations. After nearly 10 years of operation, these efficient finishing systems are still delivering consistent and reliable performance, offering unparalleled flexibility to adjust finishing needs as they evolve. Read more
John Claman, IntelliFinishing & Kasa Controls Sales & Marketing Supervisor, discusses how IntelliFinishing provides flexible finishing solutions for powder coating and liquid paint.
Automation is an integral part of any manufacturing facility, making operations smoother and more cost effective. Increasingly, next-generation finishing systems are expanding automation capabilities, allowing for efficiency, flexibility, and scalability in correlation to an operation’s requirements. In fact, there are up to five levels of automation that you can achieve in terms of historical, existing, and future systems, including the Internet of Things (IoT) devices.
Let’s look at each level of automation to dive deeper into these processes.
Levels of Automation for Finishing System
The levels of automation follow a chronological path; however, older technologies are still important today. Here are the different levels:
0-Hardwired Control
At this level, there is really very little automation, requiring almost complete operator intervention. Many conveyorized finishing systems still operate at a hardwired level of control. These include some new systems, but also, many existing systems that may be years if not decades old. These systems tend to lack flexibility and the ability to adapt, but are very robust and durable.
1-Mimic Panel
At this level, there is limited automation, and most electricians would be able to troubleshoot an issue should one occur. This level still requires a lot of operator intervention and can be costly to design and build. In fact, the use of mimic panels for automated finishing systems is quite uncommon.
2-Touch Screen Hardware Terminal
At level two, you will be able to automate most processes or simple systems using basic PLC (Programmable Logic Controllers) control systems. Replacing relays with PLCs adds flexibility (easier to make changes) and enhanced reliability in a smaller package, providing increased functionality while reducing the overall cost to design and build.
With simplified computer screen operator features, electricians trained on the equipment would be able to troubleshoot many issues. However, specialized controls programmers/engineers may be required to set up or change the PLC programming. Typically associated with the control of process items like washes and ovens, this level is very prevalent among most existing finishing systems. Some Power and Free conveyor systems are also controlled by the PLC and HMI set up.
3-PC-Based (HMIs)
With PC-level computing and operation functionality, automation opportunity increases here, including data collection and storage capabilities. Further, at this level, the integration of smart automation is possible for tasks like recipe control. There is an added expense in maintaining automation at this level due to more sophisticated control programming. However, efficiencies are gained due to simpler operation, more flexible part processing, increased reporting, and a significant reduction in manual operation.
4-Database/Web-Based
While not common in most finishing systems as of yet, many companies are moving to level 4 automation for other areas of their industrial facility—especially larger OEMs. At this level, companies are leveraging the newest software capabilities to connect the plant floor to the boardroom suite. This level starts to unite traditional Operational Technology (OT) with Informational Technology (IT). Often, companies initiate level 4 by standardizing system and locational OT processes around a unifying industrial software solution. There are fewer software programs to maintain, but software modification or unforeseen problems will necessitate the services of expert technicians and programmers.
These systems are designed to collect and access data as well as to be deployed over multiple processes or facilities for consistency, quality control, and benchmarking/data analysis. The base capabilities of some software platforms at this level can include reporting and system operation to unlimited operator terminals, the ability to handle unlimited data points (tags), and connection to an unlimited number of other software databases such as ERPs, MES, etc.
5-Fully Integrated Robotic Systems:
This level offers robotic automation for processes and conveyance.
Robotic use implies the minimization of operator engagement. Robots are often deployed in the paint booth itself for both liquid and powder systems, but they are also used to load parts on to or off of finishing systems. Typically, articulating arm robots are used for these tasks. However, reciprocating spray systems in booths, washes that adjust to part dimensions, blow off tunnels that focus in tightly on parts based on their geometry, as well as other aspects of automated systems are also forms of robotics.
To make changes or troubleshoot robots, a programmer or someone trained in the robot’s specific controlling software is usually necessary. Robots can also be controlled in conjunction with the entire finish system HMI control as part of the recipe control. The system can also collect data on the robot’s performance. And with software control, the robot operation can be replicated across multiple applications, processes or locations.
Considerations When Choosing Your Level of Automation
To discern what level of automation is right for your plant, there are several considerations to ponder. What is most important in your finishing processes?
- Better utilization of employees?
- Improved efficiency of people and equipment?
- Faster turn on finishing products?
- Safety?
- Energy savings?
- Enhanced finish management and quality control?
- Improved system flexibility to coat a wider assortment of different parts and materials?
- Increased overall visibility of operations for managers and executives?
- Preventive maintenance at the right time to significantly reduce unplanned downtime?
You should also look at historical operational data. Decisions are often driven by reliability, the integration of safety features, product rates, capacity expansiveness, the level of operator intervention that will work best, remote connection for data and support, as well as the possible integration of third-party equipment.
The level of automation must also align with the variety of pieces being finished. With increased part complexity comes the need for a highly flexible finishing system. In these situations, higher levels of automation and versatile recipe control make the most sense.
Cost is also an important consideration. While automation initially represents significant outlay, it offers rapid ROI based on lower operational expenses and improved quality. However, there are some “hidden costs” related to automation. These include the need for programming and employees skilled in the respective software, downtime due to normal computer vulnerabilities, increased demand for back-up of system data and redundancy, and operator training. Ultimately, having a programmer to keep the software running smoothly should help to save on troubleshooting or expensive outsourced programmers. Conversely, with higher levels of automation software, predictive maintenance is possible so there should be less overall unplanned system downtime.
The Future of Automation of Finishing Systems
With many impactful technologies on the horizon, the future of finishing systems automation will, of course, continue to change. These innovations include:
- Smart sensors and devices that make decisions independent of the PLC
- Artificial intelligence (AI) that will enable machine learning and decision making
- Augmented reality (AR) that will empower smartphones and other devices to produce 3-D or holographic images for training and instruction
- Emulation software to mimic operations in near real-world scenarios, much like video games
- And more!
These modern advancements will generate even more data to be stored and shared, allowing operators to make better decisions that improve the efficiency and effectiveness of finishing systems. To some extent, it will also require even greater abilities for data managers to consolidate data, report metrics in impactful ways, and employ even more sophisticated system analysis and diagnostics.
Elevate Your Finishing System
IntelliFinishing is a complete finishing systems provider that combines smart technology with our revolutionary modular conveyor for the most flexible finishing system available. This fusion of advanced engineering and progressive technology allows individual sections of the conveyor to move independently in both speed and direction, as well as to control each process via one unifying operational software that allows for per carrier recipe flexibility. A variety of manufacturers use our systems for a best-in-class finishing process. Experience it today by watching the system in action.
Finding the right solution for a company’s operations can be complex, especially when the needs are very custom. At IntelliFinishing, we offer unique solutions for powder coating systems which can be designed to meet any specific needs or requirements. One of our biggest differentiators is flexibility. Our friction-driven conveyor and smart controls deliver just that. We work with customers in many different industries and want to share with you a specific story of our work with JR Custom Metal Products, a Wichita, KS-based metal fabricator.
Why They Needed a Custom Solution
Several objectives were driving JR Custom Metal Products’ need for a new powder coat solution. They were looking to increase the quality of the paint finish for their customers. Their existing process, which was outsourced, granted the company no control over quality, often requiring considerable rework. Further, outsourcing was proving to be extremely costly, coming in at over a million a year, with slow lead times that were impacting operations. Dealing with a great variety in part sizes, JRCMP also wanted to be able to deliver the highest quality coatings based on their own values and to better meet customer turn times.
With no control over quality or delivery timing, it was time to bring operations back in-house and build a system customized to their unique needs that allowed for more cost-effective processing.
Jorge Martinez, Vice President of Sales and Marketing at JR Custom Metal Products, said, “Once we made the decision to build a powder coat finishing line, we wanted to do it right.” Doing it right involved a lot of research and time to find a seamless solution to the challenges they were facing.
The Challenge
JR Custom Metal Products required a very customized solution for powder coating because of different part sizes, thicknesses, and process times. They also needed to have the ability to stop for manual processes at the shot blast blow off platform, a de-watering station, a masking area, and for the powder coating application, while minimizing any quality defects that could occur with operators stopping the conveyor or extending manual process times. Further, they required an optional path to an automated in-line blast system.
Jorge said, “We are a job shop, and we needed a lot of flexibility. We also wanted to blast on the line, not offline. Manually blasting a heavy 10-foot long part or multiple smaller parts can take 20-30 minutes each, but with our system, we can blast 10 feet of loaded parts in as little as 30 seconds up to 2 minutes, depending on the part thickness and intricacy.”
The Solution
After a four-year process of investigation, attending PCI, FabTech, and peer group meetings where they talked with a variety of vendors and visited numerous sites with systems in place, JRCMP first chose Midwest Finishing Systems to build their system, but as their needs were explored, MFS brought in IntelliFinishing. JRCMP was particularly intrigued by IntelliFinishing’s unique flexibility, especially the cutting-edge conveyor system which was also incorporated into the design.
Martinez commented, “We use load bars that can hold up to 2,000 lbs. each. We can select dual lanes and have multiple substrates running all at one time because we can select a recipe for each particular load bar—not for the whole line. There’s not very many systems in the finishing industry that can do this.”
How the System Works
To meet all of JRCMP’s requirements, IntelliFinishing created a plan to make powder coating easier and more convenient without compromising on quality. As parts are loaded onto the carrier via load bars (custom designed by JRCMP themselves), the operator enters or selects the paint process recipe for that particular batch of parts. The ability to define, edit, and store recipes is a huge milestone for the process, determining exactly how parts will flow through the system. With a recipe-based system, each part or set of parts can receive a custom process.
Once the recipe is entered, the parts either go to an automated shot blast for cleaning or move straight to the automated part washer. If it runs through the shot blaster, it does so at the speed defined by the recipe. Heavy parts may move through the blast at 5 fpm, while lightweight parts can be sped up to help minimize the profile at faster speeds such as 10, 15 or even 20 fpm. For especially difficult parts, a recipe option can include backing the carrier up to blast the items twice.
Items then move into the automated wash that includes three stages and a dual halo final rinse of either RO water or a sealer coat. After washing and blasting, the parts stop at the blow off platform to remove any remaining water before entering a highly efficient dry off oven. In the dry off oven, parts are heated to evaporate any water residue before powder coating. Again, items may have different dry off times based on substrate and complexity, ranging from just a few minutes to 20 or even 30 minutes. From the oven, parts are directed to a temperature- and humidity-controlled environmental room.
Next up is the masking platform. This station features an HMI (human machine interface) terminal that can access specific masking instructions based on the parts arriving at the platform. As with all of the HMIs, operators can also see the entire system overview and the ability to drill into any carrier to determine present status, recipe selections, and order/part data.
Martinez remarked, “It is a smart system. We may have 10 different customers we are running on that shift, and they are all intermixed—different sizes and substrates—and it doesn’t matter. Everyone tends to base things on line speed, but our system is really based on the recipe for that one load bar.”
The operator masks each part, then they continue onto the powder paint booth where two painters apply powder paint to the parts. Once completed, the load bar releases the parts to the dual lane oven for curing, boasting 6” insulated walls to eliminate unnecessary heat loss. Having two lanes allows faster curing parts to move past slower curing parts, thus maintaining a higher level of throughput than traditional systems.
After curing, parts proceed down the conveyor to the unload station where they are unloaded for packaging and shipping. In this final step, IntelliFinishing customized the space between the oven and the unload station so that the parts have a sufficient amount of time to cool down before operator handling.
Benefits: Current and Future
Today, JR Custom Metal Products are experiencing optimized operations and agile processing. Bringing the process back inside, rather than outsourcing, has increased part control for the company, improved quality, decreased costs, and accelerated customer delivery timelines.
Unlike other non-sustainably designed powder coating systems that use overhead monorail conveyors typically limited to parts of one size and no variation in processes, JRCMP’s new system provides optimized flexibility in both part disparity and process customization. Further, for each load bar recipe process, data is collected and stored. From varying speeds through a process, or parts moved quickly through areas where no processing is required, having access to each unique recipe improves quality, consistency and throughput for similar parts that require analogous processing in the future. In addition, JRCMP users can easily manage the conveyor, equipment, processes, and recipes from three HMI terminals.
With an evolving need to process different size parts and recipes, JR Custom Metal Products turned to IntelliFinishing to provide a solution that allowed for flexibility now and adaptability in the future. Their new system provides maximum control and unparalleled customization, creating significant efficiencies that have increased throughput and decreased bottlenecks while ensuring a higher-quality end product for years to come.
Learn more about how IntelliFinishing helped JR Custom Metal Products by watching a video featuring their facility.
- Increased production 33% YOY
- Saved 24,000 sq. ft. of floorspace over other alternatives, now used for additional manufacturing production
- Dramatically reduced downtime and injuries over the previous system
- Saved significantly on labor and outsourcing of larger parts
Hytrol History
Every year, Hytrol, a leading conveyor manufacturer in the material handling industry, celebrates Loberg Day. In honor of Hytrol’s late founder, the executive leadership team at Hytrol take a break from their usual routine of meetings and strategic planning and spend the day working on the manufacturing floor with their staff. On a most recent Loberg Day, Chris Glenn, Hytrol Vice President of Operations, chose to work on the company’s powder coat and paint finishing system—its new IntelliFinishing turnkey finishing system.
“In the past, I’ve worked in fabrication and other areas, but this year I wanted to work in paint, so I loaded and unloaded parts all day,” said Glenn with a smile. “Everything was great that day. We saw really good productivity. I enjoyed it a lot. The IntelliFinishing system has been fantastic for us. I started out in sheet manufacturing 22 years ago, I’ve worked with monorail systems, and I’ve had some power and free system experience, but this is the best power & free type system I’ve ever been a part of.”
Before its installation of the IntelliFinishing system, Hytrol was utilizing an outdated power and free conveyor system. After evaluating potential replacement solutions for its old system, it was IntelliFinishing that provided the most innovative solution at the most cost-effective price, but it was not a new power and free system Hytrol would be installing. Instead, it chose a turnkey finishing system that offers a revolutionary modular conveyance and control technology that provides ultimate flexibility and superior output. For Hytrol, the result of its migration from a traditional power and free conveyor to the IntelliFinishing system, was a 33 percent increase in productivity year-over-year, a positive return-on-investment, and higher employee satisfaction.
Freeing Up Floor Space with Intelligent Systems
IntelliFinishing is committed to customizing the planning and installation of all its finishing systems. For Hytrol, it helped to design an extremely compact solution that immediately freed up floor space on the Hytrol manufacturing floor. For maximum efficiency and cost savings, it even incorporated into the plan repurposing some components of the previous power and free system that still retained some value.
“IntelliFinishing designed our current solution around our existing booths,” said Glenn. “Now we have room for one more booth and an expansion that we’re planning for next year.”
The smaller footprint of its IntelliFinishing system does not mean Hytrol has less capacity. In fact, it can now accommodate heavier production parts than it ever could with its old power and free system.
“Our system can hold up to 1,000 pounds,” said Glenn. “With power and frees, you’re often limited in the weights you can put on the line. We now have greater capabilities to paint some pretty heavy equipment that we wouldn’t have been able to paint on the line before. We would have had to paint them manually in a small booth.”
Increasing Production 33 Percent Year-Over-Year
Glenn estimates that since implementing the IntelliFinishing system, Hytrol’s overall production has increased year-over-year significantly.
“Our system has been a huge success. We wouldn’t be doing the volume we’re doing today. We’re up 33 percent over last year with the help of the system. We know we’re getting some parts off faster on the new system based on the speeds that we’re able to run, and we’re still not even at full capacity.”
Not only is Hytrol’s paint line more productive, but it is also producing a higher quality product.
“The quality of the product coming off the line is much, much better,” said Glenn. “We’re seeing about a seven or eight percent decrease in quality issues. We had so much turbulence in the old system, and we dealt with a lot of contamination.”
According to Glenn, IntelliFinishing’s decentralized drive system and the visibility it offers keeps production moving efficiently.
“With the IntelliFinishing system, if we get a carrier that’s hung up, we’re back up and running in no time,” You can’t back something up with a power and free system, but we can do that with the IntelliFinishing system. Plus, with its integrated controls, we can look anywhere in the system and see where a carrier is at, what color it’s going to be, what the drive signals are, or if we have a drive fault. The ability to go anywhere in the system and see those things is tremendous for us.”
Minimizing Downtime
Glenn estimates that with its former power and free system, Hytrol experienced a downtime of about 10 to 15 percent, which limited its productivity.
“We had jams every day with our old power and free system, which is typical of any power and free system I’ve ever been a part of,” said Glenn. “Downtime is still 5 to 10 percent even if it’s a brand new power and free system because you’ll have carrier hang-ups and different jams that you’re dealing with. With a power and free system, you have a continuous rate that your whole chain is fed. You can only speed the whole line up or down. With the IntelliFinishing system, you can slow things down based on the recipes that you have. We have some areas that are very hard to paint. With our old system, we would have to slow the whole chain down, which we couldn’t do in a lot of cases because of the throughput we needed, so we would de-dog a carrier and push it back into the booth to finish painting it. Now we can slow that part down or stop it in the booth when we need to.”
An Increase in Labor Productivity
Hytrol has also seen an improvement in its work-in-progress at assembly.
“Our first pass yields went up about 10 percent after implementing IntelliFinishing,” said Glenn. “A lot of it has to do with the pre-verification coming out of fabrication. You can see any of those carriers anywhere. You know exactly how many carriers you’ve got left on that particular card. We’re able to track that information so much better. Now, our assembly line staff can say, ‘I need this FO, when is it going to be ready?’ And we can look exactly where it is in the system and estimate when the part is going to come off.”
Glenn estimates that Hytrol’s staff is notably more productive using the IntelliFinishing system.
“We’re seeing about a 10 to 15 percent labor savings,” said Glenn. “We are using more labor because we have more lift stations and can paint in all three booths at the same time, which is something we were not able to do with our old system. However, if you look at our overall labor number today, compared to the volume we were producing previously, we’re able to maintain a lower percentage of labor based on production volume.”
Even more impressive, the Hytrol staff are exceeding their previous productivity rates working fewer days each week.
“With our previous system, we were working seven days a week,” recalls Glenn. “Now, we only work five to six days per week and the only reason we’re working so many Saturdays is just to support the other production areas. There have been several days this year that we were able to send some people home from our paint unit because we’ve done so well with the IntelliFinishing system.”
A Positive Return on Investment
Not only has the IntelliFinishing system allowed Hytrol to increase its production, but it has also reduced some of its ancillary costs.
“The cost of the oil for our old power and free chain was tremendous,” said Glenn. “Our previous power and free system was 21 years old, so we had to put so much oil on it just to keep it running. With the IntelliFinishing system, we don’t need the expensive oil anymore. Also, the last year that we ran our old power and free system, we outsourced $1.6 million worth of powder. We had to send a truck to Memphis to have it painted. Now, we’ve brought all that work back in-house.”
Freedom from Conventional Power and Free Systems
For the paint system staff at Hytrol who are instrumental in the success of its operations, the transition from a conventional power and free system to the IntelliFinishing system required some initial adaption. However, having spent a year enjoying the greater productivity of the IntelliFinishing system, Glenn’s staff report they never want to go back to a conventional power and free system.
“There was a lot of apprehension at first, getting used to the HMIs, but now if you ask any of our employees who work on our paint system, they’d never want to go back. They are comfortable on the HMI’s now, and they like that they can look ahead to what carrier is coming and what color it is. They are excited about our future expansion and the other solutions we’re looking at.”
According to Glenn, IntelliFinishing’s commitment to customer service and its quality solutions are an important factor in Hytrol’s continued partnership with IntelliFinishing and Kasa.
“IntelliFinishing has been great to work with. During the implementation, they were there for us every step of the way. IntelliFinishing and Kasa remind us a lot of Hytrol and how we support our customers. No matter what, we’re going make sure our customers are satisfied, and IntelliFinishing did that for us too.
- Increased production 33% YOY
- Saved 24,000 sq. ft. of floorspace over other alternatives, now used for additional manufacturing production
- Dramatically reduced downtime and injuries over the previous system
- Saved significantly on labor and outsourcing of larger parts
Hytrol History
Every year, Hytrol, a leading conveyor manufacturer in the material handling industry, celebrates Loberg Day. In honor of Hytrol’s late founder, the executive leadership team at Hytrol take a break from their usual routine of meetings and strategic planning and spend the day working on the manufacturing floor with their staff. On a recent Loberg Day, Chris Glenn, Hytrol Vice President of Operations, chose to work on the company’s powder coat and paint finishing system—its new IntelliFinishing turnkey finishing system.
“In the past, I’ve worked in fabrication and other areas, but this year I wanted to work in paint, so I loaded and unloaded parts all day,” said Glenn with a smile. “Everything was great that day. We saw really good productivity. I enjoyed it a lot. The IntelliFinishing system has been fantastic for us. I started out in sheet manufacturing 22 years ago, I’ve worked with monorail systems, and I’ve had some power and free system experience, but this is the best power & free type system I’ve ever been a part of.”
Before its installation of the IntelliFinishing system, Hytrol was utilizing an outdated power and free conveyor system. After evaluating potential replacement solutions for its old system, it was not a new power and free system that provided the most innovation solution at the most cost-effective price. Instead, it was IntelliFinishing, a turnkey finishing system that offers a revolutionary modular conveyance and control technology that provides ultimate flexibility and superior output. For Hytrol, the result of its migration from a traditional power and free conveyor to the IntelliFinishing system, was a 33% increase in productivity year-over-year, a positive return-on-investment, and higher employee satisfaction.
Freeing Up Floor Space with Intelligent Systems
IntelliFinishing is committed to customizing the planning and installation of all its finishing systems. For Hytrol, it helped to design an extremely compact solution that immediately freed up floor space on the Hytrol manufacturing floor. For maximum efficiency and cost savings, it even incorporated into the plan repurposing some components of the previous power and free system that still retained some value.
“IntelliFinishing designed our current solution around our existing booths,” said Glenn. “Now we have room for one more booth and an expansion that we’re planning for next year.”
The smaller footprint of its IntelliFinishing system does not mean Hytrol has less capacity. In fact, it can now accommodate heavier production parts than it ever could with its old power and free system.
“Our system can hold up to 1,000 pounds,” said Glenn. “With power and frees, you’re often limited in the weights you can put on the line. We now have greater capabilities to paint some pretty heavy equipment that we wouldn’t have been able to paint on the line before. We would have had to paint them manually in a small booth.”
Increasing Production 33% Year-Over-Year
Glenn estimates that since implementing the IntelliFinishing system, Hytrol’s overall production has increased year-over-year significantly.
“Our system has been a huge success. We wouldn’t be doing the volume we’re doing today. We’re up 33% over last year with the help of the system. We know we’re getting some parts off faster on the new system based on the speeds that we’re able to run, and we’re still not even at full capacity.”
Not only is Hytrol’s paint line more productive, but it is also producing a higher quality product.
“The quality of the product coming off the line is much, much better,” said Glenn. “We’re seeing about a seven or eight percent decrease in quality issues. We had so much turbulence in the old system, and we dealt with a lot of contamination.”
According to Glenn, IntelliFinishing’s decentralized drive system and the visibility it offers keeps production moving efficiently.
“With the IntelliFinishing system, if we get a carrier that’s hung up, we’re back up and running in no time,” You can’t back something up with a power and free system, but we can do that with the IntelliFinishing system. Plus, with its integrated controls, we can look anywhere in the system and see where a carrier is at, what color it’s going to be, what the drive signals are, or if we have a drive fault. The ability to go anywhere in the system and see those things is tremendous for us.”
Minimizing Downtime
Glenn estimates that with its former power and free system, Hytrol experienced a downtime of about 10 to 15%, which limited its productivity.
“We had jams every day with our old power and free system, which is typical of any power and free system I’ve ever been a part of,” said Glenn. “Downtime is still 5 to 10% even if it’s a brand new power and free system because you’ll have carrier hang-ups and different jams that you’re dealing with. With a power and free system, you have a continuous rate that your whole chain is fed. You can only speed the whole line up or down. With the IntelliFinishing system, you can slow things down based on the recipes that you have. We have some areas that are very hard to paint. With our old system, we would have to slow the whole chain down, which we couldn’t do in a lot of cases because of the throughput we needed, so we would de-dog a carrier and push it back into the booth to finish painting it. Now we can slow that part down or stop it in the booth when we need to.”
An Increase in Labor Productivity
Hytrol has also seen an improvement in its work-in-progress at assembly.
“Our first pass yields went up about 10% after implementing IntelliFinishing,” said Glenn. “A lot of it has to do with the pre-verification coming out of fabrication. You can see any of those carriers anywhere. You know exactly how many carriers you’ve got left on that particular card. We’re able to track that information so much better. Now, our assembly line staff can say, ‘I need this FO, when is it going to be ready?’ And we can look exactly where it is in the system and estimate when the part is going to come off.”
Glenn estimates that Hytrol’s staff is notably more productive using the IntelliFinishing system.
“We’re seeing about a 10 to 15% labor savings,” said Glenn. “We are using more labor because we have more lift stations and can paint in all three booths at the same time, which is something we were not able to do with our old system. However, if you look at our overall labor number today, compared to the volume we were producing previously, we’re able to maintain a lower percentage of labor based on production volume.”
Even more impressive, the Hytrol staff are exceeding their previous productivity rates working fewer days each week.
“With our previous system, we were working seven days a week,” recalls Glenn. “Now, we only work five to six days per week and the only reason we’re working so many Saturdays is just to support the other production areas. There have been several days this year that we were able to send some people home from our paint unit because we’ve done so well with the IntelliFinishing system.”
A Positive Return on Investment
Not only has the IntelliFinishing system allowed Hytrol to increase its production, but it has also reduced some of its ancillary costs.
“The cost of the oil for our old power and free chain was tremendous,” said Glenn. “Our previous power and free system was 21 years old, so we had to put so much oil on it just to keep it running. With the IntelliFinishing system, we don’t need the expensive oil anymore. Also, the last year that we ran our old power and free system, we outsourced $1.6 million worth of powder. We had to send a truck to Memphis to have it painted. Now, we’ve brought all that work back in-house.”
Freedom from Conventional Power and Free Systems
For the paint system staff at Hytrol who are instrumental in the success of its operations, the transition from a conventional power and free system to the IntelliFinishing system required some initial adaption. However, having spent a year enjoying the greater productivity of the IntelliFinishing system, Glenn’s staff report they never want to go back to a conventional power and free system.
“There was a lot of apprehension at first, getting used to the HMIs, but now if you ask any of our employees who work on our paint system, they’d never want to go back. They are comfortable on the HMI’s now, and they like that they can look ahead to what carrier is coming and what color it is. They are excited about our future expansion and the other solutions we’re looking at.”
According to Glenn, IntelliFinishing’s commitment to customer service and its quality solutions are an important factor in Hytrol’s continued partnership with IntelliFinishing, a division of Kasa.
“IntelliFinishing has been great to work with. During the implementation, they were there for us every step of the way. IntelliFinishing (and Kasa) remind us a lot of Hytrol and how we support our customers. No matter what, we’re going make sure our customers are satisfied, and IntelliFinishing did that for us too.”
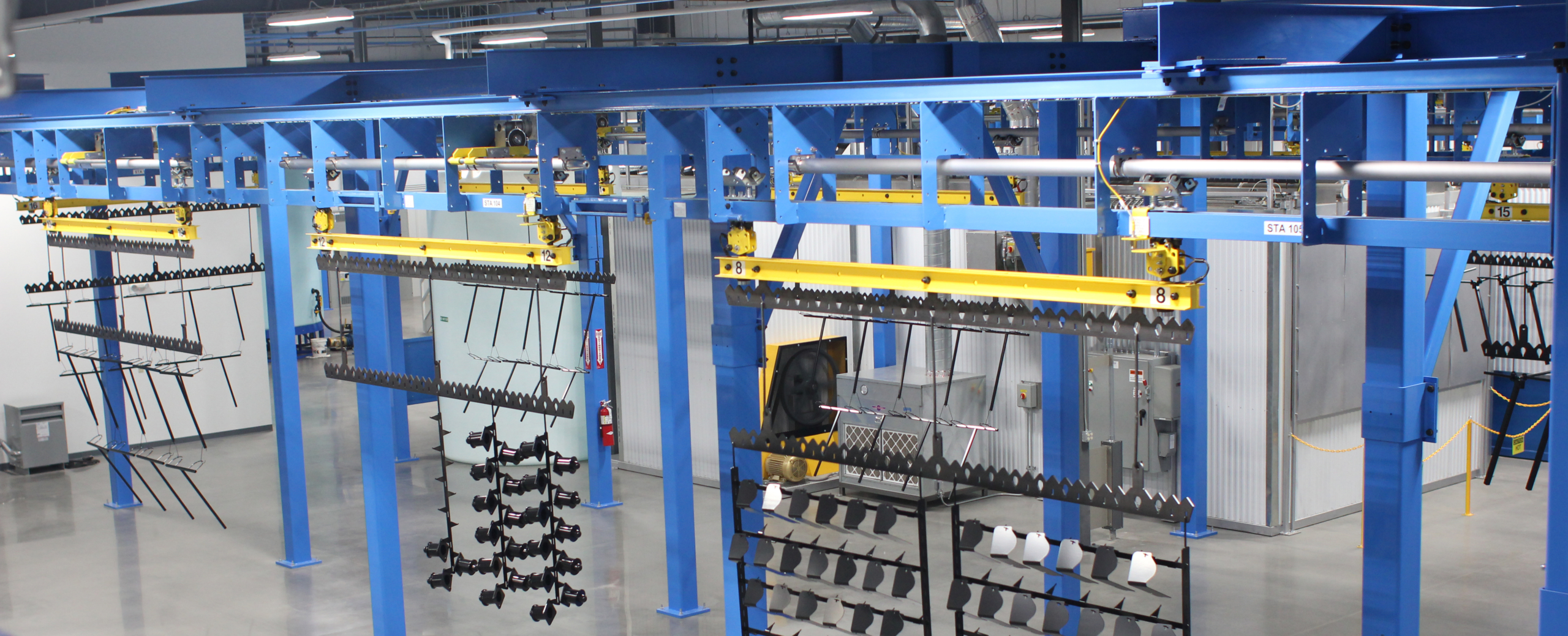
In the past ten years, there have been major changes in the finishing industry that affect process times. In addition, the demand in most industries has fluctuated significantly. Manufacturing trends, including lean methodology, have changed our traditional method of processing parts. How do you design a paint system that is flexible and will handle the uncertainty of the future?
Sign up for this free Products Finishing Webinar, presented by IntelliFinshing’s John Claman, to review the latest in overhead conveyor technology for paint systems — friction-driven conveyors.
We will review case studies of how friction-driven conveyors, teamed with smart controls, offer flexibility and expandability and have challenged traditional monument paint systems.
Registrants will learn:
- Difference between friction-driven conveyor & traditional overhead conveyors
- How IntelliFinishing systems are responsive to future changes
- Key questions to determine if a friction-driven conveyor is right for you
- How to remove transportation waste by integrating your paint system and manufacturing processes with point of use delivery
Register for the webinar here.
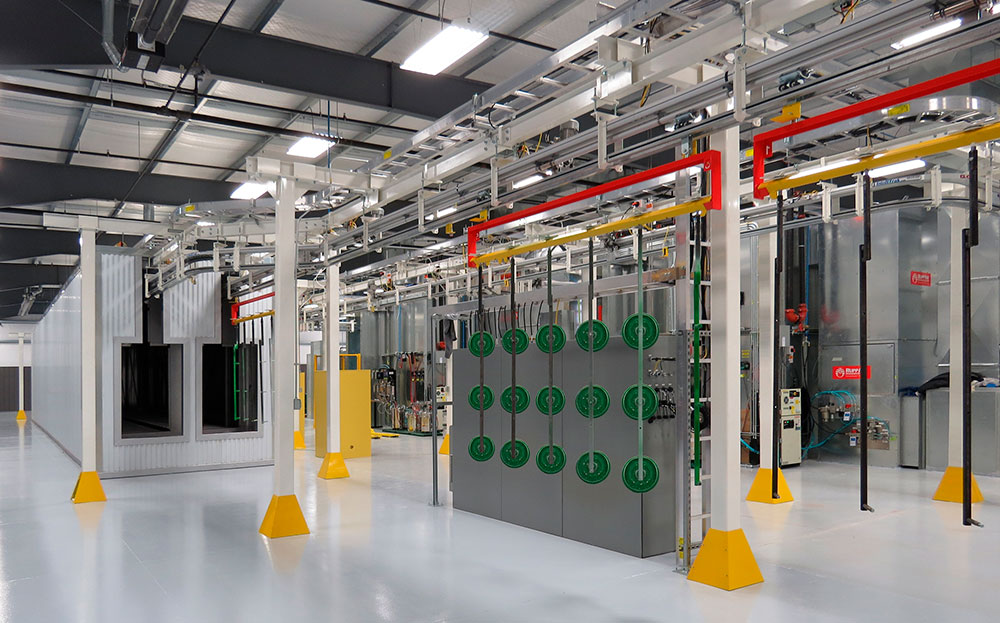
The beginning of any success story starts with an idea. About four years ago, the Albers brothers of Cheney, Kansas, came upon an opportunity to paint pulleys for a company that manufacturers agriculture equipment. The brothers developed a business plan based on the manufacturer’s need, and from there, Albers Finishing & Solutions was launched. New to the industry, the Albers brothers started their research online to find a finishing system that would meet their vision. Fortunately, they came across IntelliFinishing, and right away, they recognized an offering that was unique to the market, providing both part flexibility and high-quality outcomes. Here’s their story of finishing success.
Why a Unique Solution Was Imperative
When creating their infrastructure, the Albers had several design considerations relating to space and process requirements. They also knew that they needed a system that required less labor, providing cost-effective efficiency.
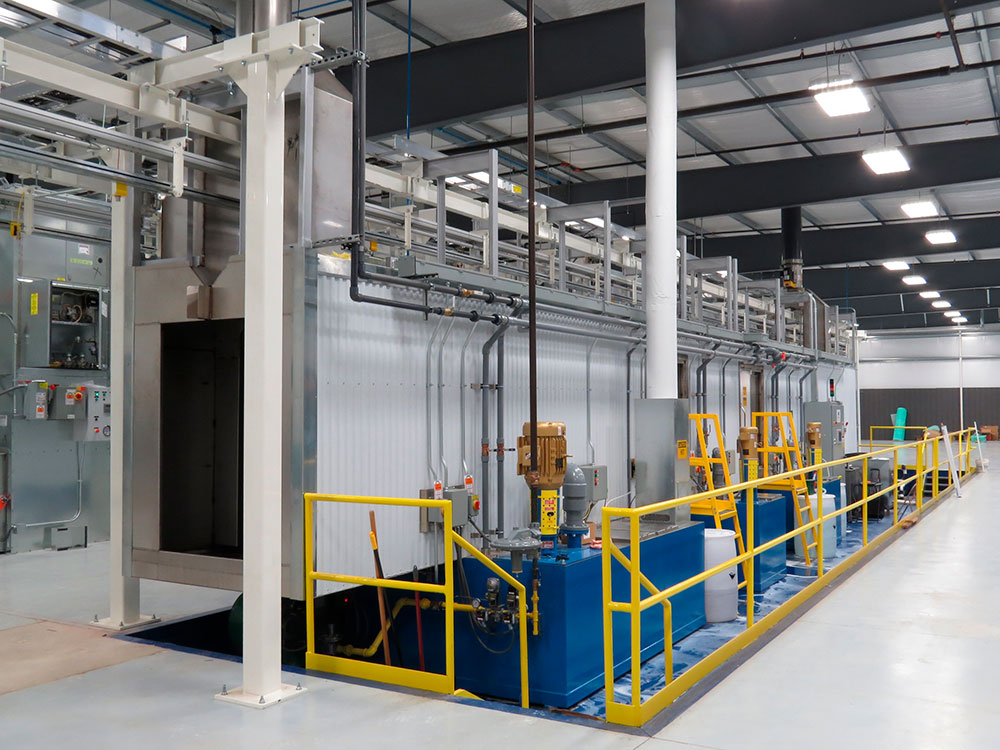
Bret Albers said, “We wanted an automated liquid paint system that would require only a couple of people to run it, fit in our space, and provide an excellent finish. We worked with IntelliFinishing from the start, and they helped us achieve our vision.”
How and Why the IntelliFinishing System Works for Albers
Meeting the Alber’s need for minimal labor, the IntelliFinishing system necessitates only two operators in full auto, and they mainly serve as loaders and unloaders. Once the pulleys or other parts are loaded, the carriers first hit the wash station and move on to the blow-off area. From there, they circle back around to the dry off oven, then head to the primer booth. In this booth, a robot paints each part.
Albers said, “Not only did IntelliFinishing integrate the programming of the robot with the system, but they also used spinners built by Albers on the carrier so each side of the product can be fully painted, requiring only one robot per booth.”
Offering maximized flexibility for parts of varying sizes, when products are larger than a matrix of pulleys, the carrier can back out of the booth and do a T-turn so that the other side of the part can be processed. After priming, parts head to the top coat booth which features another robot. Depending on the part parameters, the programming can be easily modified. However, the system also has the ability for manual painting as well.
“Often, part batches are of minimal quantity that doesn’t justify the need for reprogramming of the robots. For these loads, we simply place a person into the spacious booth to complete the painting,” Albers added.
After the paint is applied, the carriers move to a dual lane cure oven where heat can be adjusted depending on the thickness and size of parts. After curing, the carrier arrives at the load area where the finished product is unloaded.
In addition to its superior part adaptability and automation that requires less labor, the IntelliFinishing system also saved the company valuable floor space. There are two deadhead turns in the system, allowing carriers to turn in a smaller area. The automated 3 stage wash and dry off ovens which run parallel to each other are much closer than typically possible with a chain system.
Albers added, “Our cure ovens are closer to our paint booth line, too. And should we need more capacity in the future, the system was also designed to be expandable—we can add additional paint booths in a line along the present line of booths, or other process equipment and functions as the need arises.”
More Unique Features of the Liquid Paint System
The IntelliFinishing Liquid Paint System created for Albers Finishing & Solutions runs with a friction-driven rotating tube, not a chain, allowing the system to run both forward and in reverse. Carriers can also stop at any point while the rest of the line moves through other processes. The modular washers have separate wash sections which can be programmed independently by part need. Advanced controls track, monitor, and guide each part through its specific process, offering both higher quality and leaner operations. Another bonus for the Albers is IntelliFinishing’s energy-efficient ovens which can save users up to 49% in energy costs versus non-insulated units.
Albers Brothers Reflect on Their System
The system has been in place now for a few years, and the Albers brothers are quite satisfied with their investment. In this time, the IntellFinishing system has allowed Albers Finishing & Solutions to deliver quality parts finishing while keeping costs at a minimum.
Albers said, “When we work with new parts, sometimes we have to play around with the recipe. With the IntelliFinishing system, we can easily move parts back into the booth without impacting other processes. This system does so many things a chain system cannot. In fact, if someone were to literally give me a completely free chain-based system rather than purchasing the IntelliFinishing system, I would not take it!”
“Since its initial installation,” Albers continues, “our
business has grown, and IntelliFinishing has been right there to support us
with new software controls and capabilities that will allow us to expand the
system in pace with our growth. We look forward to continuing to work with
IntelliFinishing as our business thrives.”
Does your business have a similar challenge? See how our Liquid Paint System
works by watching our video. Then contact us to talk about
how we can create a custom solution for you.