Organizations consider many factors when considering a painting or coating finishing system. The capabilities of the system and its design are critical to performance. One area to pay close attention to is maximizing part density. Traditional chain conveyors come up short here, with most requiring 6-inch spacing or more between parts. A flexible solution with smart controls, like the IntelliFinishing System, is a game-changer for part density, with racking as a key ingredient.
In this post, you’ll learn what part density is, how to maximize it, and how racking plays a role.
What Is Part Density, and Why Is It Hard to Achieve with Chain-Based Conveyors?
Part density describes the ability to hang parts tightly together on a system. Monorail systems typically have poor density. Items must hang from hooks on the chain, spaced from a few inches to even feet apart. Loaders hang parts as the chain moves by at a set speed. For high-speed operations, loaders must scramble to keep up with the chain. As a result, they often must place relatively small pieces a far distance from one another, which creates big gaps and low part density.
The only way to increase part density in this scenario is by preloading parts offline onto a removable load bar and then hanging a whole raft of parts at once. It can be challenging with a constantly moving chain system. There is sometimes the ability to stop the chain for loading, but it’s not without unintended, negative impacts downstream. Those impacts can include issues with the timing of pretreatment stages of a wash, travel through a shotblast, time in ovens, the timing of the processing of parts in the paint booths, and of course a drag on total throughput.
Because these systems literally chain you to a speed with a given amount of time to hang, you’ll constantly fight the part density battle.
Maximizing Part Density and Stop Chasing the Chain
The solution is to stop chasing the chain! Power and free systems and the IntelliFinishing system have the ability for carriers to halt, receive loads, and rejoin the main line. However, there are differences between these two concerning part density.
The IntelliFinishing System enables smooth acceleration and deceleration because a VFD (Variable Frequency Drive) motor control for each track section. Power and free conveyors use motors that control long chain sections, each typically having a specific speed. In this situation, a carrier “dedogs” from one chain at one pace and then “dogs” onto another chain at another rate. The effect of this is parts swinging considerably, which has its own set of concerns.
Why Is Maximizing Part Density So Critical in a Finishing System?
Maximizing part density results in finishing more products in less time. When the finishing time is less, you save on natural gas, electricity, and labor, so your total cost to finish per square inch decreases.
It all comes back to the ability to pack parts closer, which you can do more consistently with the IntelliFinishing System. Typically, spacing can be as little as a few inches, so you’ll be processing more parts per hour. There’s also almost no part sway. The gains in efficiency can range from 10-30%. But to further optimize, you’ll need to have the proper racking, too.
How Racking Supports Part Density
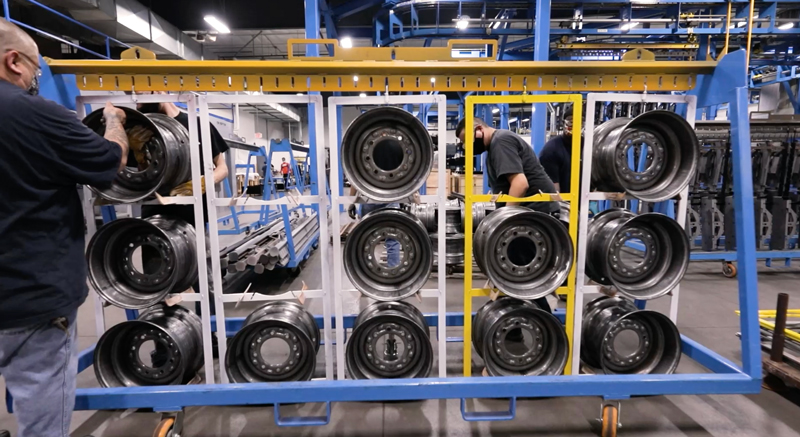
Racking is the key to part density. You won’t have great part density if racking prevents parts from hanging tightly. For example, one of our system customers, JR Metal Fabrication, designed their own racking that greatly maximizes part density. Their setup includes a vertical hanging bar with slots at specific distances. From this, horizontal bars fit within the slots to create a grid. Each horizontal bar has an approximate spur spaced every few inches from which parts hang. The spurs, rails, and hanging bars come in a variety of sizes and arrangements to work with many different types of parts. This rail and slot hanging rack system allows JR Metal Fabrication to maximize part density on their 10-foot carriers. They routinely place from 20 to as many as 800 parts on each carrier.
How Can You Use an IntelliFinishing System for Racking and Increase Part Density?
We don’t provide the racking with our systems. It’s usually the responsibility of the system owner. However, we have a system that allows for greater part density than traditional chain-based overhead conveyor based finishing systems. The racking should be appropriately sized and fitted for the parts you finish and for the size of carrier you need on your system.
Are There Ever Situations Where Part Density or Racking Don’t Matter?
The answer is—they always matter. There may be instances where part density is fixed for some reason. An example is our customer, Prince Hydraulics, which paints hydraulic cylinders and valves. They determined they always hang only eight cylinders vertically per carrier, which is 8 feet long. Each cylinder is about a foot apart.
Cylinders can be an inch or two in diameter to several inches. Their lengths vary, too. Their system spins cylinders using star gears as they emerge from the wash, move through the blow-off device and, arrive in the paint booth in front of robotic paint applicators.
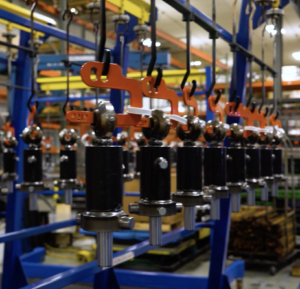
In theory, they could hang more than one cylinder. However, the spinning effect would cause lower cylinders to wobble if daisy-chained to the top cylinder. To mitigate this, they choose to go with eight cylindrical products per carrier only. However, they also paint hydraulic valves. When painting valves they hang between 4 to 8 valves vertically per each of the 8 foot hook spaces. In this way they can paint from 24 to 80 valves per 8-foot carrier. Depending on the size of the valves, each vertical rack creates a space between the valves from several to just a couple inches apart. The vertical rail still spins during the blow off and within the booth. Because the valves attach to the rail, the spin is controlled, and the robotic paint program adjusts to finish each valve. The part information at each hanging spot on the carrier is transferred from their ERP where it’s recorded in production when the parts are hung on removable loadbars resting on carts and then transferred to their IntelliFinishing system when the removable bar with parts are being loaded. The part information then is communicated to the robotic program through their IntelliFinishing Recipe system. This technique allows Prince to load up to 80 valves per carrier, depending on the size.
Maximize Part Density with a Full Plate
The IntelliFinishing System is an innovative take on finishing systems. It’s chainless, agile, and has the capabilities to increase part density and capitalize on great racking. All the ingredients come together so your business can fill up on total finish efficiency. Contact us to see if an IntelliFinishing system might be right for you.