Automation is Vast Industry and Kasa Plays a Small but Specific Role
The word automation has many different definitions. To some, automation may mean faster, better. To others, automation may mean higher productivity. To us, automation encompasses that and more. The International Society of Automation defines it as “the creation and application of technology to monitor and control the production and delivery of products and services.” And we absolutely agree.
While the automation industry is vast, Kasa Controls and Automation is proud to play a small role in the global industry. We believe the automation profession is not just about machines but about the people involved in the process of creating and applying revolutionary technology. Our outcomes are clear: produce and deliver products and services to the highest standards.
What is Industrial Automation?
Industrial automation uses set technologies and devices to operate and control industrial processes. With superior performance, industrial automation provides systems with safe, sustainable, and economical operations.
Often, industrial automation includes utilizing computer software or even robotics and can increase productivity while reducing costs. Industrial control systems allow users to operate locally or remotely, providing flexibility while ensuring quality.
At Kasa Controls and Automation we are automation experts, not process experts. We don’t focus on designing devices, making prototypes, or providing equipment. We do something more.
How We Fit
We know the systems. As experts, we automate the equipment provided by others and integrate material handling systems. While we aren’t a fit for everyone, we see the value we bring to others through our work.
Automation provides benefits to various industries, including manufacturing, transportation, utilities, and facility operations. Automation is often attributed to higher efficiency and productivity rates while encompassing improved safety mechanisms in the workplace.
Automation’s improved safety has been shown to help avoid and reduce injuries in the workplace by using data and quick communication outputs that allow the operator to adjust accordingly.
Automation also provides users with increased systems control, leading to faster product and data throughput, smarter accuracy, and system reliability.
We know that automation helps businesses improve. Human error can be the cause of an expensive or fatal mistake. Slip-ups happen, but most can be avoided. Automation provides more data input and output, which can decrease human error in the industry by delivering cross-referencing, complete synchronization, and repetitive computing.
Besides automating production and conveyorized systems, we can also help lower system costs. For example, businesses often assume high energy costs cannot be avoided. However, utilizing innovative controls and automation technology, which provides analytical capabilities along with data processing, facilities can manage their energy usage and costs more effectively. Accurate performance metrics are vital to analyzing energy usage. We’ve pioneered smart controls that provide communication and data about utility usage for the grain industry and other facilities. These data rich programs not only enhance understanding of utility usage, they can help operators or even the equipment itself cycle on in ways to avoid peak loads and other conditions that significantly increase monthly utility costs.
Kasa Controls and Automation also knows how to utilize our expertise and the benefits of automation to log preventative maintenance and help with predictive maintenance, which in turn can help prevent downtime. We help companies in a wide variety of industries to automate and improve throughput, reduce costs, enhance quality, and improve safety.
Automotive
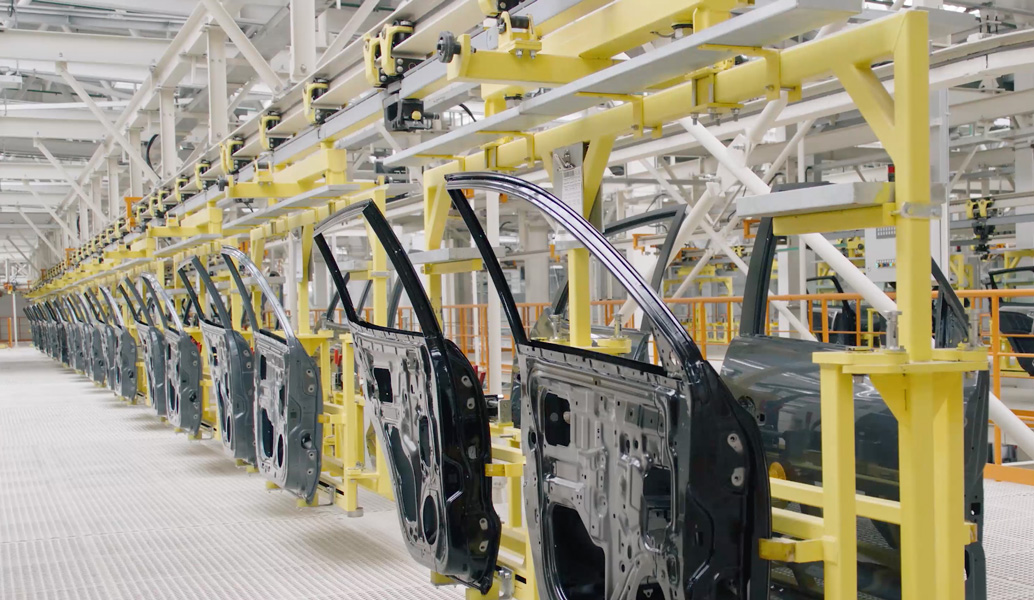
The U.S. automobile industry is worth over $80 billion and accounts for roughly 3% of the U.S. GDP. Facilitating, managing, and producing cars plays a vital role in supporting the economy. An automotive manufacturing plant will often contain a wide variety of conveyors used to move the car body along mechanisms while it is in the building process.
At Kasa, we do not provide the conveyors or the equipment, but we know how to control these systems and tools using PLCs, HMIs, various software and other control equipment, so they do their jobs as intended. These controls help ensure the material or the car is handled safely and efficiently during the manufacturing process.
Grain
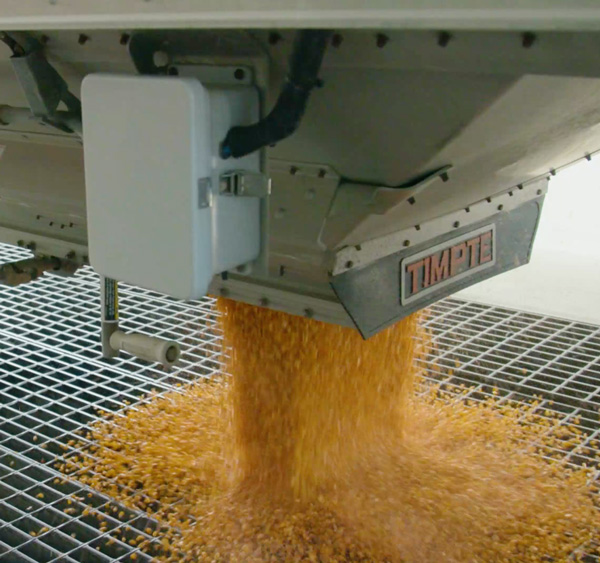
Grain facilities also rely on conveyor belts similar to the automotive industry to move commodities throughout their facilities. The plant needs to correctly choose the path the grain must follow in order to store it in the correct location to maximize the mix of grains and obtain the greatest potential profit for the facility. Since grain dust is also potentially explosive, all systems need to be closely monitored for safety. Kasa has created software to manage the entire operation of many grain facilities. Through that software we can integrate with the hazard monitoring systems common in today’s grain elevators. Our software communicates to and with each piece of equipment in the grain handling system to functionally operate at the correct time, in a safe manner, to move the grain to or from storage appropriately while removing the chances of errors common when these items are done manually without automation.
Kasa’s software helps prevent mixing commodities, alerts operators of potential dangers before significant damage, and allows systems to run automatically and often with less personnel in grain facilities from small to extremely large. We often also help reduce grain facility utility charges related to peak demand by sequencing on equipment so peak loads are diminished as well as other forms of utility monitoring.
Industrial Paint Systems (via IntelliFinishing)
Kasa’s dba IntelliFinishing is a complete conveyorized finishing systems provider. Our unique finishing system supplies new levels of automation to the industrial paint industry, including for powder coating and liquid painting applications. With IntelliFinishing, individual carriers of parts on the conveyor can operate independently of other carriers throughout the entire system. The system relies on smart control technology and our modular, friction-tube based, conveyor.
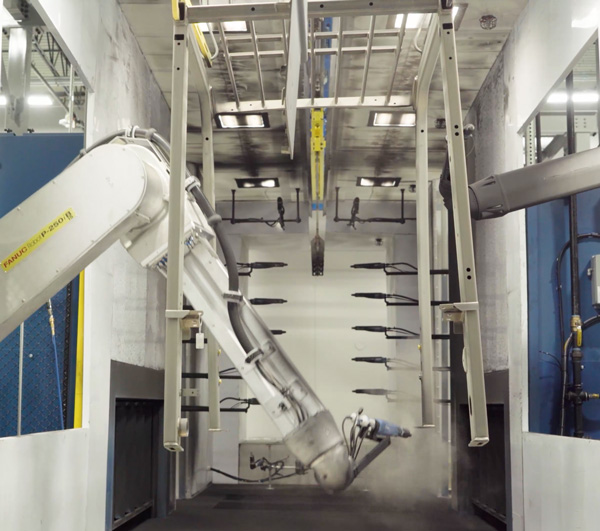
IntelliFinishing systems use carriers racked with parts to be painted that move throughout the system based on recipe instructions for each carrier. The recipes dictate how long a carrier will remain in each process throughout the system. Our smart control system dictates carrier speed, direction, and process steps at any point within the system. These capabilities mean that the system can slow down or stop in process areas and speed up in non-process zones. We can even direct parts to move along different pathways, backwards, or laterally depending on the conveyor design. Ultimately, this provides a system that can finish a much wider assortment of parts than traditional conveyorized options since each type of part is processed based on the recipe most appropriate for it, whereas traditional overhead conveyors rely on chains that link all parts hung together. Traditional finishing conveyors offer very little ability to change a part’s recipe.
IntelliFinishing systems are most popular within the metal finishing industry, and the system’s flexibility has allowed users to create products with the highest quality in finish, with higher throughput, and with the ability to change process or even grow the systems over time based on changing finishing needs.
Baggage Handling
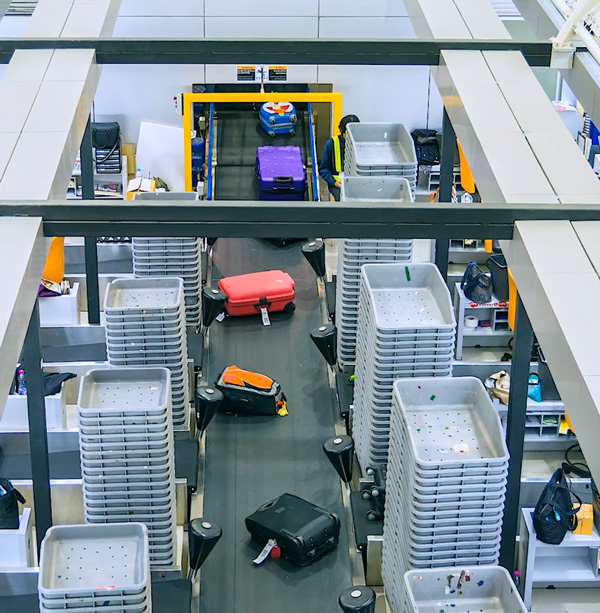
Air travel and airports have an abundance of moving parts to their operation system – literally and figuratively. One important aspect of a trip is to make sure the customer’s belongings get to and from the right place at the right time.
Integrating our smart controls into baggage handling conveyor systems allows greater flexibility and automation in checking weight, baggage counting and sorting, and following rigorous security measures. Our unique design allows for a more manageable and productive system. This helps airport operations run more smoothly and travelers to receive their belongings on time.
Parcel
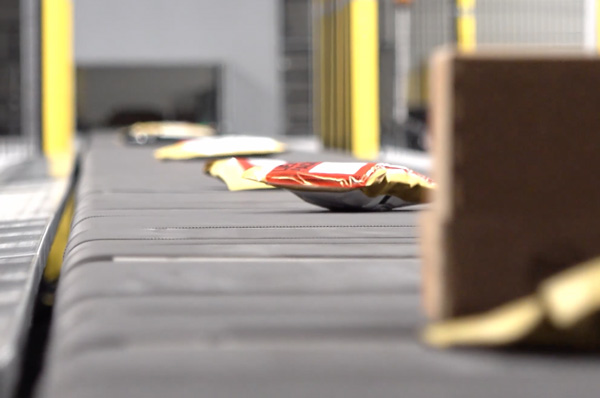
We recognize that thriving industries have many moving parts, and we’re here to help speed that along. Kasa Parcel Automation provides the operational controls for many parcel delivery and fulfillment industries. Our controls act as the brain behind the conveyors that control parcel movements and allow companies to streamline the conveyance of their inventory.
Our controls operate efficiently at high capacity, but they also help automate the sortation process, ensuring quality part or product distribution performance and on-time delivery.
Panel Build
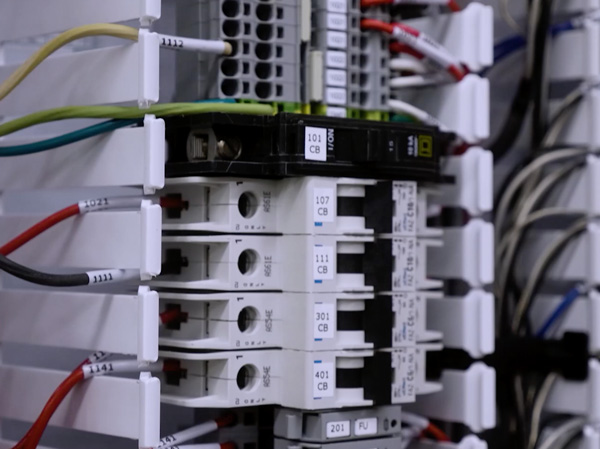
At Kasa, we recognize the value of well-built, organized control panels in any controls or automation system. These systems cannot operate without the support of well-made control panels. Our 40,000-square-foot shop is dedicated to building panels. The panels used and implemented in automation combine PLC’s, VFD’s, I/O, comm devices, electrical and data wiring, and switch technologies to allow operators to control entire systems. We also build the HMI’s (Human Machine Interfaces) with touch-screen computer displays that are the means through which systems are operated by facility personnel.
Our panels are built with our customers in mind – we understand the importance of perfect detail, organized panels, labeled wiring and components, and safe operation using high voltage. Our panels meet with industry compliance standards and offer customization to meet the level of specifications required by even the most demanding of customer needs.
Why Kasa?
The automation world is vast, growing, and busy. Although Kasa plays only a modest part in that world, our expert knowledge and experience is vital to the industry.
Automotive, agricultural, industrial paint, baggage handling, parcel distribution, fulfillment centers, and panel build are just a few of the areas and industries that we have and will continue to help flourish.
We recognize automation is “more than meets the eye”. When done right, it seems…well, automatic and easy. At Kasa, we will continue to seek to revolutionize the automation industry by applying our custom designed smart controls. From control panel builds to projects requiring critical automation services and products, Kasa Controls and Automation has a wide breadth of experience and expertise to help you with your automation needs. Contact us for more information about any of our offerings.